Emergency lighting regulations
Compliance has never been easier
With many barriers to compliance, from high maintenance costs to time-consuming testing requirements, it’s no surprise many buildings and businesses fall short of emergency lighting regulations.
Building owners and managers are becoming increasingly aware of emergency lighting compliance, as they look for solutions that reduce risk and minimise the sky high costs associated with staying compliant. All the while, protecting their building occupants from potential hazards and avoiding hefty fines and lawsuits.
Fortunately, recent advancements in emergency lighting technology and systems are making compliance easier, more affordable, and more accessible than ever before. So, let’s talk about some opportunities building managers and owners have to improve their emergency lighting compliance and reduce costs.
Three key areas to focus on
1. IMPROVING LUMINAIRE PERFORMANCE
One area of compliance involves meeting the minimum requirements for light level in a particular area. When you choose a high-performing product, you can achieve compliance with fewer light fittings, while minimising the cost of installation and ongoing maintenance.
2. USING MODERN BATTERY TECHNOLOGY
You can further reduce the cost of ownership (while staying compliant) when you choose a product that uses the right type of battery.
Some estimates show a total saving of over 50% when you choose a longer-lasting battery (although this will vary depending on the battery type). We pioneered lithium batteries in emergency lighting, which last 2-3 times longer than the older style NiCd batteries. With our L10 products, the battery has a service life of 12 years+ - this is phenomenal performance for a self-contained product!
With a longer lasting battery, you’ll also experience fewer failures, lowering the risk of your emergency lighting system not operating correctly, and maximising the number of working, compliant fittings at all times.
3. MOVING TO AUTOMATED TESTING SYSTEMS
The majority of emergency lighting installations need to be manually tested each month, which is where most compliance issues originate. These include:
Inefficiency
Manually tested systems require you to flick a switch at a switchboard or a key switch to manually test and inspect each fitting. You also have to time this right so that you view the fittings at the right time to check for compliance. This inefficiency means it can take weeks to complete all the testing on a large site.
Lack of time
Meeting the required level of compliance can be quite onerous for the end user. The problem with this is that facilities staff have a lot of other responsibilities and contractors are always pressed for time. Other reactive maintenance activities often take priority. It’s one major reason why compliance so often lapses and the yearly or monthly tests aren’t carried out.
Poor recordkeeping
Manual systems usually mean manual logbooks. This can lead to inconsistent recordkeeping where the tests may be done, but the record isn’t kept up to date. Or the logbook is updated but the test hasn’t been performed properly (or at all). So, it’s not surprising that one of the main areas where people fail an audit is not having correct test records in place.
Cost
There’s also a high cost associated with compliance when you rely on manual testing processes. The more time it takes to test and maintain your emergency lighting system, the more it’ll cost.
Fortunately, with recent advancements in technology, there’s a solution to these problems. An automated testing system can help maintain compliance, ensuring all your fittings are tested regularly and records are automatically updated in the system. It will highlight any luminaires that need maintenance repairs so you can ensure that all your fittings are ready to operate when needed - all with minimal effort and risk, at the lowest possible price.
How XT HIVE impacts compliance
Our team of engineers developed the XT HIVE system to make compliance easier, with a focus on testing and reporting. Here’s how the compliance requirements are impacted by HIVE:
Regular testing
First of all, the six monthly function test to confirm that the luminaires are still operational is a breeze with XT HIVE. You can schedule this test ahead of time and the system will automatically perform the discharge test and report back. You’ll get a confirmation that the fittings are all installed and operational, all without visiting them in person or physically flicking key switches to put them into discharge mode. The system does it all for you - all you need to do is arrange any maintenance that’s needed. With a manual system, visiting each individual emergency light fitting and visually checking that it works for the full minute could take hours or days in a large building. But with HIVE, this process is almost instantaneous.
The six monthly function discharge tests can be scheduled to take place automatically at a time that’s convenient for the end user. Reports are made available at the click of a button - all within minutes.
With XT HIVE, you can group and segment your fittings and schedule them for testing at any time you want. An automatic system is always on, so you always have wireless access to your fittings, and it will run the tests for you based on your predetermined schedule.
Availability
Each time you perform a discharge test, the fittings will need around 24 hours to recharge before it’s available at full capacity again. If you test all the fittings in a floor at once, for example (common practice when manually testing), this could leave your building occupants with a much shorter duration of emergency lighting in the event of an immediate, genuine power outage.
With automated testing, you can choose what fittings go into test mode and when. For example, you might do every second fitting on one night, and every other fitting the next night. This means you can minimise the risk during the recharge period for buildings that are occupied 365 days a year.
Support
Our free LTS Program ensures customers get full support and maximum benefits from their investment over the lifetime of the product. While the system is simple and intuitive, support is still important part of compliance for:
- System health checks
- Expert advice to help optimise Zoneworks
- Ongoing training
- Free software upgrades
- Dedicated point of contact
This support service is completely free of charge for the life of the system.
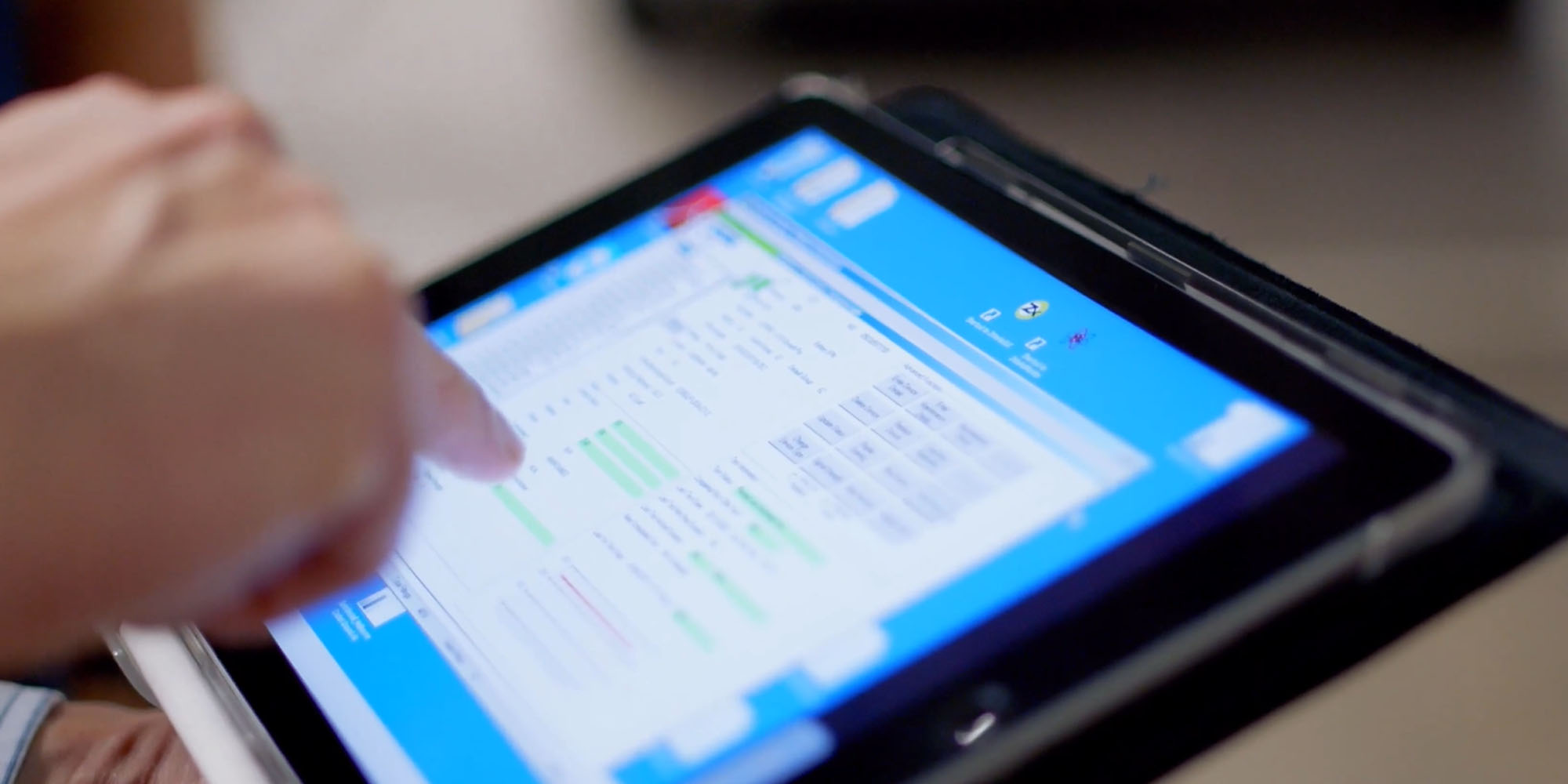
Ready to learn more about XT HIVE?
Think HIVE might be the answer? If you want to ensure your emergency lighting systems are compliant without all the headaches associated with manual testing, you need Zoneworks XT HIVE. Check out our Zoneworks HIVE website or contact us for a chat and let our team assist with your next project.
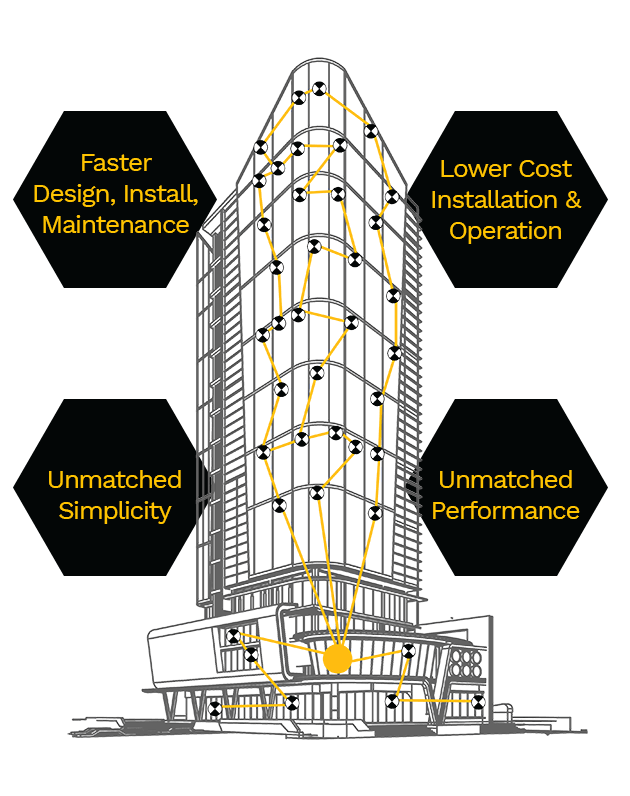