Emergency and exit lighting is a life safety requirement that requires ongoing testing and reporting to ensure legal compliance.
Without the right solution, it can be costly and inconvenient to manage, with manual logbook entry and, unfortunately, a significant number of fitting replacements occurring on a six-month basis.
However, many opportunities exist to address and better manage compliance challenges and improve the lifecycle of emergency lighting. Many sustainability initiatives can be adopted to reduce the carbon footprint of healthcare facilities; these include:
-
Replacing old technology luminaires with new low-energy and long-life alternatives
-
Using more environmentally friendly battery technology like Lithium Nanophosphate
-
Reducing the amount of fittings required with a lighting audit and design
-
Moving to a fully remotely managed testing and monitoring system
-
Installing a wireless system to remove cabling requirements
-
Using paperless and remote commissioning
The good news about these initiatives is that they can be implemented easily as incremental changes rather than a full upfront investment. Many facilities persist with inferior solutions, spending significant money on maintenance to stay compliant and continuing to support an emergency and lighting solution that is working against a low-carbon future.
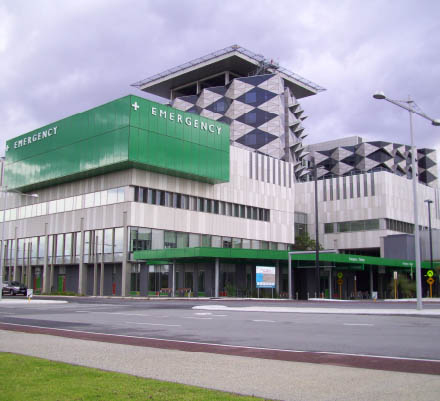
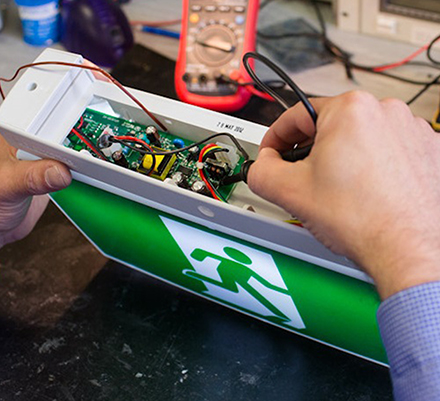
Let’s look at these initiatives in more detail:
1. Luminaire technology
Selecting products that are designed to provide maximum life is crucial in compliance-based applications, especially in hospitals where the interruption of patients and access to sterile areas is best avoided. The key areas to consider around lifetime include:
1. The Design life of the product and the parameters used to determine lifetime. This is critical as many products assume an ambient temperature lifetime, but this doesn’t consider the environments these products operate in, hence why 40 degrees is a far more important measure to benchmark against. Check the testing credentials of your products, not just the warranty.
2. Then there is the battery component, which is very well known in the emergency lighting world as a fitting's Achilles heel. This is about the battery’s characteristic of retaining charge and then discharging correctly over time. Battery technology like Lithium Nanophosphate has proven to outperform the life of other components of the luminaires by a significant value. This type of technology is no longer a maintenance burden. Older battery technologies like NiCd and NiMH have inferior performance but are also manufactured with toxic heavy metals that are harmful to the environment.
3. There are opportunities to reduce energy in emergency lighting luminaires, especially with existing installations using fluorescent tubes or LED fittings with poor Lumen/Watt efficacy. This is most prevalent in car parks, stairwells, and back-of-house areas that use batten and circular-type fittings. Improvements in LED lifetimes and drivers have resulted in significant energy savings.
4. Different classifications of emergency and exit luminaires provide opportunities to optimise the design and installation, ensuring the least amount of fittings are used within the building. Ask for an emergency lighting audit and design to determine the best solution.
2. Emergency lighting testing and monitoring systems
The majority of emergency lighting installations need to be manually tested every six months, which is where most compliance issues originate. These include:
1. Inefficiency and added travel - Manually tested systems require you to flick a switch at a switchboard or a key switch to test and inspect each fitting every 6 months manually. This requires a person or team to be onsite for the 90-minute duration test and mark the logbook with the testing result. This inefficiency means it can take weeks to complete all the testing on a large site, causing unnecessary travel. Fortunately, with recent advancements in technology, there’s a solution to these problems. An automated testing system can help maintain compliance, ensuring all your fittings are tested regularly and records are automatically updated in the system. It will highlight any luminaires that need maintenance repairs so you can ensure that all your fittings are ready to operate when needed - all with minimal effort and risk, at the lowest possible price.
2. Wireless RF systems—With the advancement of RF wireless technology, hard cabling the emergency lighting system to each fitting is no longer required. Advanced systems now run off one controller to wirelessly connect up to 1000 fittings. Fewer cables result in less embodied carbon being added to each facility. After installation, the commissioning of the system can be completed remotely without the need for paper documentation once again, reducing the need for additional travel to and from a site.
3. Using data to inform decision-making - Monitored systems can make it easier to manage and track fitting lifecycle because of the data retained within the system. Information such as fitting commissioning dates, service activities, and battery performance over time all help to provide information to the facility engineer. Assessment of the data can then enable them to more accurately plan replacement activities and provide opportunities to extend the luminaire operation rather than simply replacing them after a set operating period.
4. Use existing infrastructure – Monitored systems require software to operate which traditionally means the installation of a dedicated server computer on-site that has network cabling to the monitoring system controllers. By utilising a building’s existing network infrastructure and a common or shared server environment (either on-site or in the cloud), the installation, operation, and management of the dedicated server hardware can be eliminated thus saving power and lifecycle replacement (typically every 4-5 years).
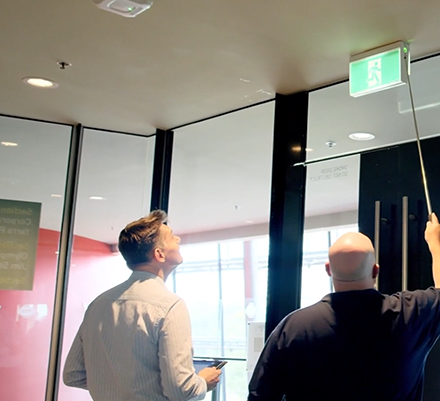
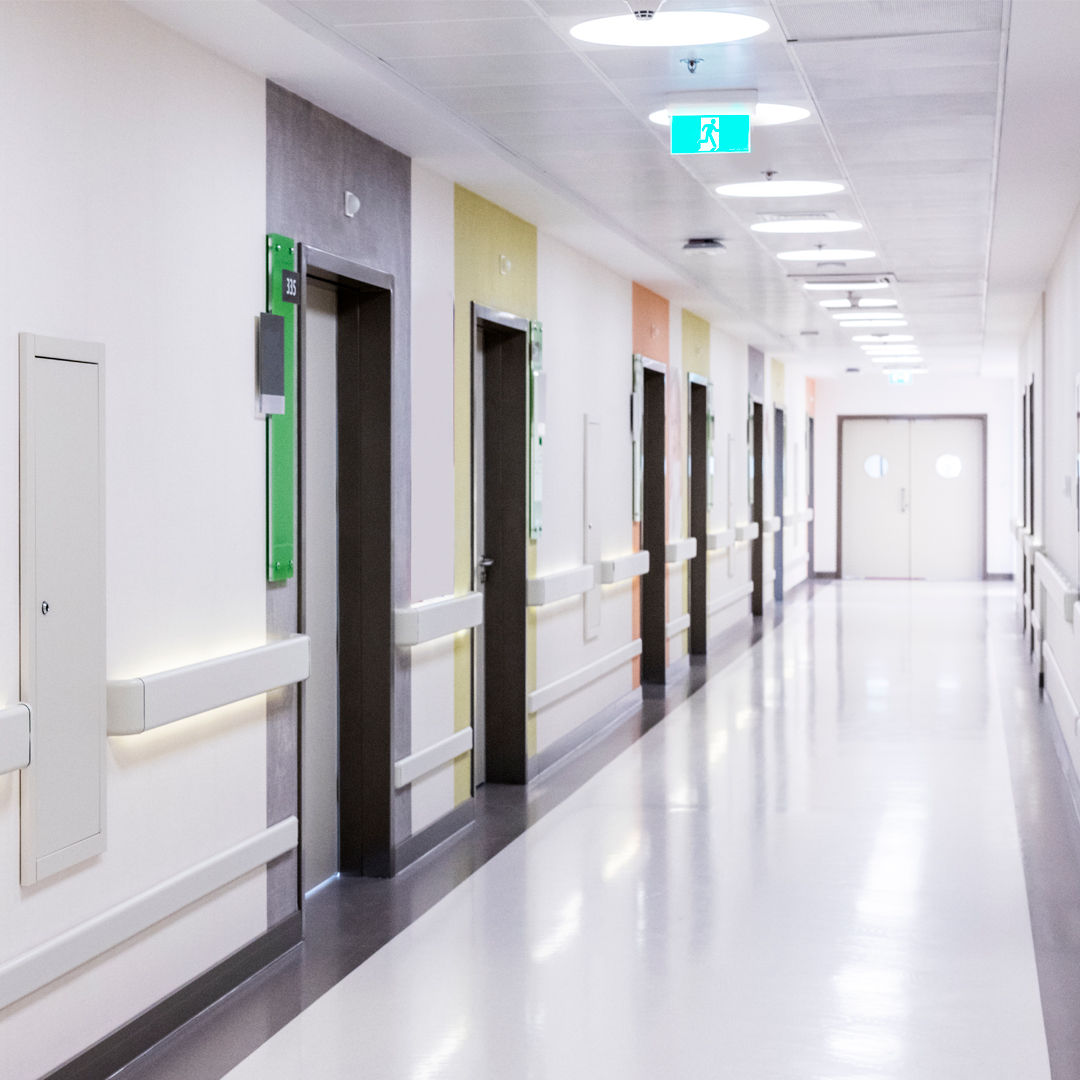
Another consideration to ensure the long-term performance of emergency and exit lighting is the support for your chosen products and system. Access to spare parts will mean that damaged fittings or failed components can be replaced so that the fitting service life can be maintained for as long as possible. From a systems perspective, it’s important to consider backwards and forward compatibility. Forward compatibility means that you can keep operating the system that is in place while taking advantage of new technologies and features with minimal or no additional infrastructure investment – delivering continuous operation of the system over a long period of time.
Implementation—Compliance is expensive when you rely on old luminaire technology and manual testing processes. The more time it takes to test and maintain your emergency lighting system, the more it will cost. Fortunately, recent technological advancements have provided a solution to reducing our carbon footprint and moving to a more sustainable future.
But how do we achieve this in a capital-constrained environment like healthcare?
With older emergency and exit lighting luminaires and testing systems, each six-month test will result in repairs and replacements, and this is the time to begin an incremental upgrade to a new sustainable solution.
The system will be fully upgraded by progressively replacing fittings using repairs and maintenance budgets with long-life fittings with automatic testing capability over 2 -3 years. This, combined with the simple addition of a controller, will mean the site has a fully automated testing and monitoring system with no additional cabling, luminaires with a maintenance-free profile of 12 years, and reduced operating energy across the site.
The sustainability outcomes are measured by:
-
A reduction in energy consumption
-
A reduction in fitting replacements going to landfill
-
A reduction in travel to the site for six monthly testing
-
No toxic metals are being used in batteries
-
Less cabling required for wireless testing systems
This is also the time to make sure that the contractor doing the work is following best practices with the disposal of any end-of-life product. The recycling rate for end-of-life emergency lighting batteries is unknown but is likely to be very low – it is estimated to be just 5%. Programs such as Exitcycle and Flurocycle have been set up to assist with ensuring that end-of-life emergency and exit lighting batteries and fluorescent tubes are collected, recycled, and processed. Have a conversation with your contractors and suppliers to ensure that end-of-life product is disposed of appropriately.
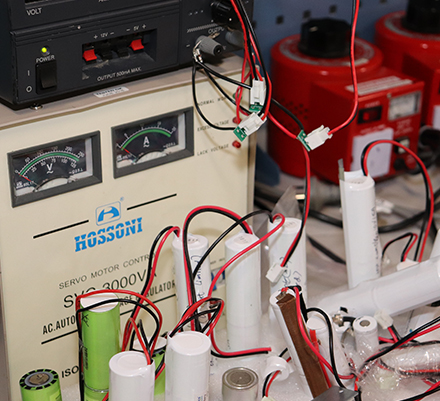
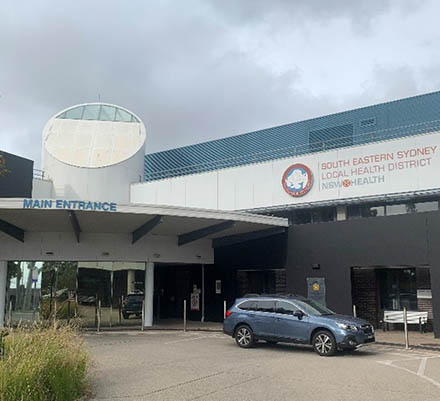
Real-world insight
Many healthcare facilities are already addressing their emergency lighting challenges through automated testing and implementing strategies for progressive upgrades using fittings that increase efficiency and reliability. One such case is Sutherland Hospital in NSW, Australia.
The Sutherland Hospital and Community Health Service is approximately half an hour's drive south of Sydney, in the suburb of Caringbah. Established in 1958, it is a major metropolitan hospital and teaching hospital with 375 inpatient beds. As with many hospitals, it has undertaken many extensions and renovations over the years, resulting in various emergency lighting products and systems being used within the building. These ranged from manually tested fittings to various automated systems. A modern monitored emergency and exit lighting system was first introduced to Sutherland Hospital in the Stage 1 capital works upgrade and has proven to be the system of choice for Stage 2 works. ACIA Electrical Services was tasked with conducting this latest upgrade and the remaining buildings with an expansion to the system.
Before the upgrades, the hospital's emergency and exit lighting systems were outdated and inconsistent with current standards. The existing lighting fixtures were inefficient and unreliable and posed potential risks in an emergency. Recognising the importance of maintaining a safe environment for patients, staff, and visitors, the hospital management invested in a modern, technologically advanced solution.
The Challenge
Complete emergency lighting upgrades of large or multiple buildings require significant planning and budgeting and can sometimes be financially out of reach. Sutherland is no different, so the ability to incrementally upgrade was important. The biggest challenges for Sutherland were multiple systems, testing regimes, spare parts and replacement products, and general support for the incumbent systems.
Emergency lighting systems are notorious for being inoperable if they are not supported with training and know-how. Sutherland has been constantly challenged around baseline data, managing the constant maintenance of older NiCd battery-powered fittings, and maintaining testing and compliance records. The goal was to remove the burden around emergency and exit lighting compliance and reduce ongoing maintenance costs. Cameron from ACIA commented, “For something like emergency lighting, you must make it simple for installers and facility managers to understand. If it’s complicated, compliance and testing won’t happen without a whole heap of pain and money”. “At the end of the day, Sutherland Hospital needs to have confidence that we are leaving them with a system that does what it is supposed to do and is supported when required”. He added.
For Mark Deluca, Sutherland Hospital Engineering and Maintenance Manager, “Patient and staff safety are paramount to the Hospital. However, the challenge of rising emergency and exit light fitting failures meant that getting replacement parts was becoming more difficult, and maintenance costs continued to increase. We needed a reliable and easy solution within the constraints of a busy operating hospital”.
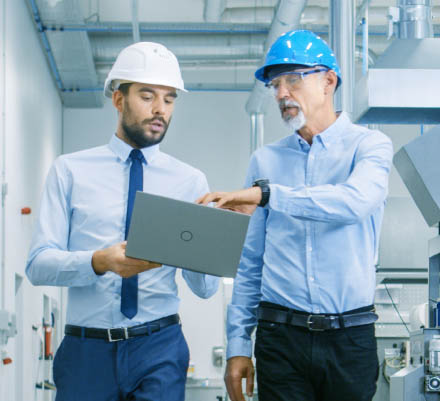
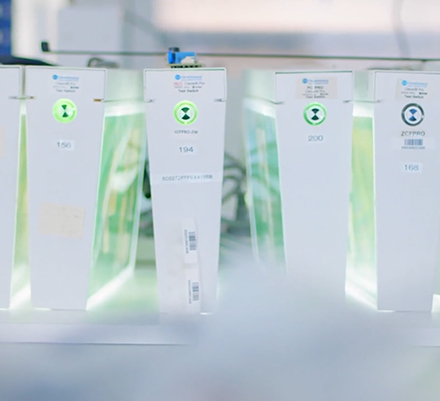
Solution
After carefully evaluating available options, the hospital upgraded its emergency and exit lighting systems to a monitored system utilising RF communication technology between fittings. The system offered several advantages over traditional systems, including:
• Advanced automatic testing capabilities: The luminaires continuously monitor their performance and report issues in real time, ensuring compliance and reliability.
• Energy efficiency: The LED technology used in the luminaires consumes significantly less energy and have a longer design life than previous emergency lighting, resulting in cost savings and reduced environmental impact.
• Easy installation and maintenance: the systems innovative design simplifies installation and maintenance tasks, minimising disruptions to hospital operations.
• Longevity and reliability: the luminaires are built to withstand the rigours of a healthcare environment and are backed by comprehensive warranties and lifetime support for peace of mind.
Stage one of the Sutherland Hospital Emergency Lighting upgrade was completed with a lithium battery-backed exit, emergency luminaires, and a sophisticated software testing system with excellent results. The advantage of the RF system selected is that each new upgrade extends the system, allowing the hospital to continue building the system with less complexity and more certainty around emergency lighting compliance. “The support around commissioning and ensuring the system works 100% is vital in installing emergency lighting”, says Cameron. “Support from vendors is critical as it ensures we deliver to Sutherland Hospital the best outcome, both installation-wise, the final outcome, and how the system operates on an ongoing basis”.
So far, over 800 RF emergency luminaires have been installed across two stages. Because additions to the communications infrastructure are so easily achieved, future stages will be rolled out following compliance testing of existing luminaires and planned capital works. This allows the hospital to reduce capital budgets because fittings will be replaced gradually as part of the hospital's day-to-day maintenance operation.
Results
Cameron from ACIA Electrical found the overall process seamless. “It was important to have the manufacturer support to complete this project with limited interruption to the hospital. This was achieved by planning the installation and commissioning and not requiring additional cabling or backbone hardware. We have now installed a state-of-the-art emergency lighting system for Sutherland Hospital that has simplified compliance testing and set the hospital up for further system expansion”
The upgrade to the RF-monitored emergency lighting technology has yielded significant benefits for Sutherland Hospital:
• Enhanced safety: The new emergency lighting system provides reliable illumination in an emergency, ensuring the safe evacuation of patients, staff, and visitors.
• Improved compliance: The system’s automatic testing capabilities help the hospital comply with relevant safety regulations and standards.
• Energy and maintenance savings: The reliable and efficient LED technology of the lithium-backed luminaires has reduced energy consumption and lowered the hospital's operating costs.
• Minimal disruptions: The seamless installation process minimises disruptions to hospital operations, allowing critical services to continue without interruption.
Mark Deluca, Sutherland Hospital's engineering and maintenance manager, says, “The implementation of a modern RF emergency and exit lighting system as an upgrade has been relatively painless, especially given that we have a busy aging hospital. The minimal infrastructure requirements and factory support provided to ACIA gave us great comfort to undertake the emergency lighting upgrade as part of our operational maintenance strategy”. He goes on to say, “We are already seeing the results with simplified compliance testing and the reassurance that we have long life fittings that won’t need to be touched for many years to come”.
The upgrade of Sutherland Hospital's emergency and exit lighting system to modern RF emergency and exit lighting technology represents a significant investment in safety, compliance, efficiency, and sustainability. By leveraging the advanced features of a modern RF emergency and exit lighting solution, the hospital has enhanced its ability to provide a safe environment for patients, staff, and visitors while realising cost savings and ensuring compliance with regulatory requirements. These successfully staged upgrades serve as a model for other healthcare facilities seeking to modernise their emergency lighting infrastructure.
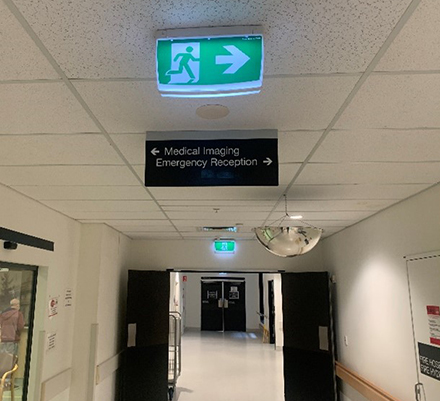
Conclusion
In conclusion, the implementation of modern emergency and exit lighting systems presents a pivotal opportunity for healthcare facilities to enhance safety, improve compliance, and advance sustainability efforts. This paper has underscored the critical role of emergency lighting in ensuring life safety and legal compliance within healthcare settings while also highlighting the challenges associated with traditional manual testing methods and outdated technology.
However, amidst these challenges lie numerous opportunities for improvement and innovation. By embracing sustainability initiatives such as transitioning to low-energy, long-life luminaires, adopting environmentally friendly battery technologies like Lithium Nanophosphate, and implementing wireless monitoring systems, healthcare facilities can meet compliance requirements and reduce their carbon footprint and operating costs.
Moreover, the paper has outlined a strategic approach to implementation, emphasising the feasibility of incremental upgrades over time rather than a significant upfront investment. By progressively replacing outdated fittings with modern, automated solutions, facilities can streamline testing processes, reduce maintenance burdens, and achieve long-term sustainability goals.
Real-world examples, such as the successful emergency lighting upgrade at Sutherland Hospital, further demonstrate the tangible benefits of modernising emergency lighting infrastructure. Enhanced safety, improved compliance, energy savings, and minimal disruptions to operations are among the key outcomes observed, reinforcing the value of investing in advanced technologies and solutions.
Overall, this paper serves as a call to action for healthcare facilities to prioritise the modernisation of their emergency lighting systems. By leveraging innovative technologies, strategic planning, and industry best practices, facilities can ensure the safety and well-being of patients, staff, and visitors and contribute to a more sustainable future for healthcare environments.