When the ten-year onsite Marvel Stadium test results were being processed to determine the performance outcome of L10 Nanophosphate, two guys already knew what the results would be.
Michael Duce and Matthew Beattie have been running the long term testing program at Clevertronics since 2009. The program constantly monitors the performance data from a wide range of luminaires on continuous test in both standard and elevated ambient temperatures.
We asked them to share some insights into the long term test facility at Clevertronics. We started with what long-term testing is and how the collected long-term data is used?
Matthew explained, "Long term testing is about understanding how well our design intentions and the methods we used to build products actually perform. I guess it's a view into the service life of a product which assists us to tweak or make changes based on the performance outcomes."
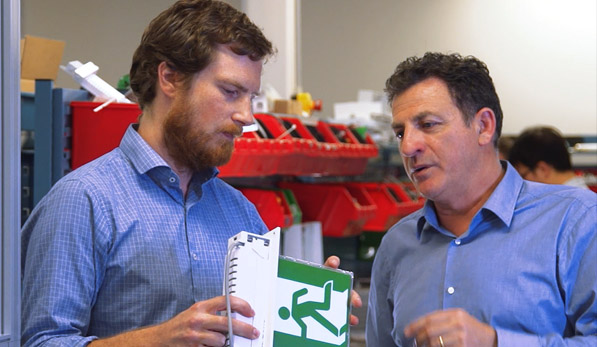
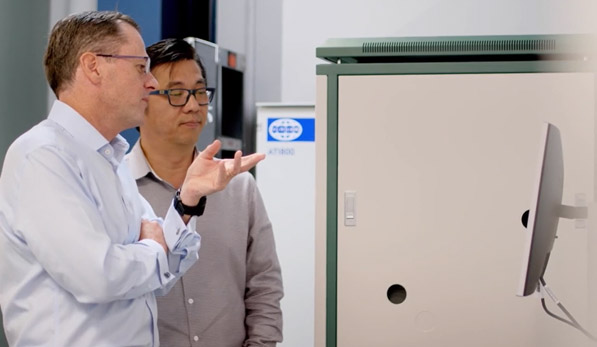
There are two key benchmarks we evaluate;
-
Design Life which is the operational time frame we expect from the unit, and
-
Service Life is based on the actual data you collect about the product over a certain length of time in real life conditions.
Importantly, our design life is based at a 40°C external ambient, which we realise sounds onerous and even ambitious for some markets. Still, it's essential to understand how your products perform above the expected ambient temperatures.
Service life and design life are interrelated because you have design criteria at 40°C external ambient, but in reality, it's going to run in environments that are far more conducive to a longer operational lifetime. This becomes your service life based on real time results in real applications across the world.
L10 Nanophosphate is an excellent example. Our 40°C external ambient design life compared to the average real-life 25°C ambient temperatures experienced at Melbourne's Marvel Stadium.
After 10 years, 97% of the original products have not required any maintenance, providing us with the actual service life thus far. Based on these current results, people are now asking, "Well, how long will L10 last?" While we won't make full-service life predictions just yet, we do have the continuous test data of the L10 batteries beginning in the Lab from 2009. These are still operational after 13 years, proving that L10 exceeds the 10 year design by some considerable margin.
We continue to collect and analyse the data, which is fed into the design process to make adjustments, improvements or enhancements as part of our continuous improvement process.
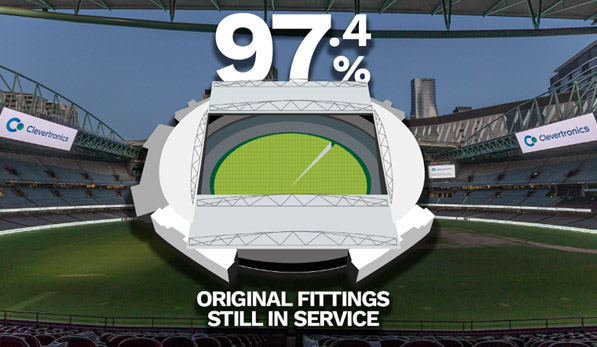
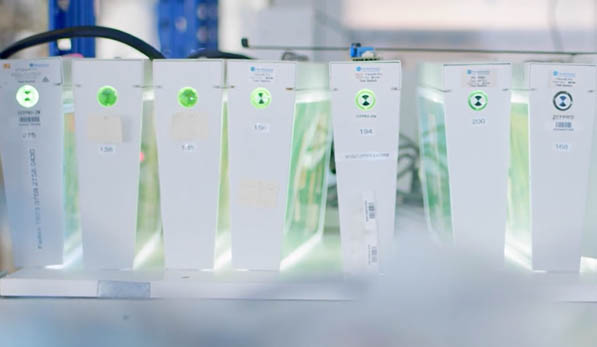
Michael Duce joins in when we review products and components tested & analysed to provide insight into possible failure points.
We look at the entire product's whole makeup, but I will start with the LED lamps. The LEDs' performance and ability to produce the light output required to be compliant is assessed in our photometry laboratory. To understand lamp degradation, we review the in situ LED performance against the baseline products of its type when they are new.
Another area that can be a little bit tricky on the electronic side is the electrolytic capacitors. Specific calculations have been proven over the years to be reasonably accurate in determining the lifetime of a capacitor which can affect service lifetimes. With our constant analysis, we can select the size, class type and manufacturer to suit the design lifetime.
Then there is the battery component which is very well known in the emergency lighting world as a fitting's Achilles heel. This is about the battery's characteristic to retain charge and then discharge correctly over time. We've seen it at Marvel Stadium, where charge retention is an incredible 95% after 10 years of continuous operation. There's about to be the third generation of L10 battery that outperforms all earlier generations, which is quite scary considering the incredible results we are already realising.
This is where comparing lab data and actual life data is so important. We can look further into the future based on our incremental improvements.
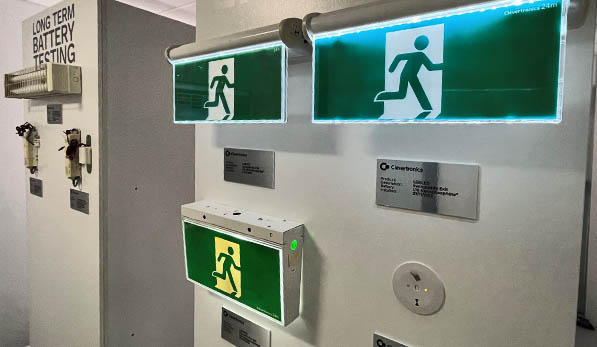
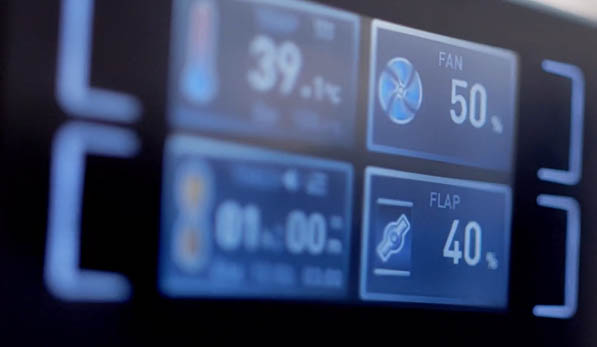
The final one is assessing the performance of the housings and materials of the products. In our long term test facilities, we've seen some plastics that have deteriorated due to exposure to high temperatures or UV. This has allowed us to test and research the quality of our plastics and improve the material selection based on this experience. We do equivalent accelerated testing now, almost an extension of the long term test lab. Suppose we see something that looks discoloured or not performing quite as well as it should. In that case, we assess the product and identify possible alternative materials in an accelerated UV test chamber.
We often hear that the quality of our products is well and truly felt by those installing them, and the reliability is demonstrated in the service life outcomes. As product designers and developers, that tells us that our investment in our long term testing program is assisting in achieving outstanding results for everyone.
Ready to find out how we can help you with your next project?
Want to know more about how to choose the best emergency lighting solution for your next project? We’re here to help so contact us today and find out how the Clevertronics team can assist with your next project.